Hyperion & AFC combine expertise to offer new high-performance carbide rod solution
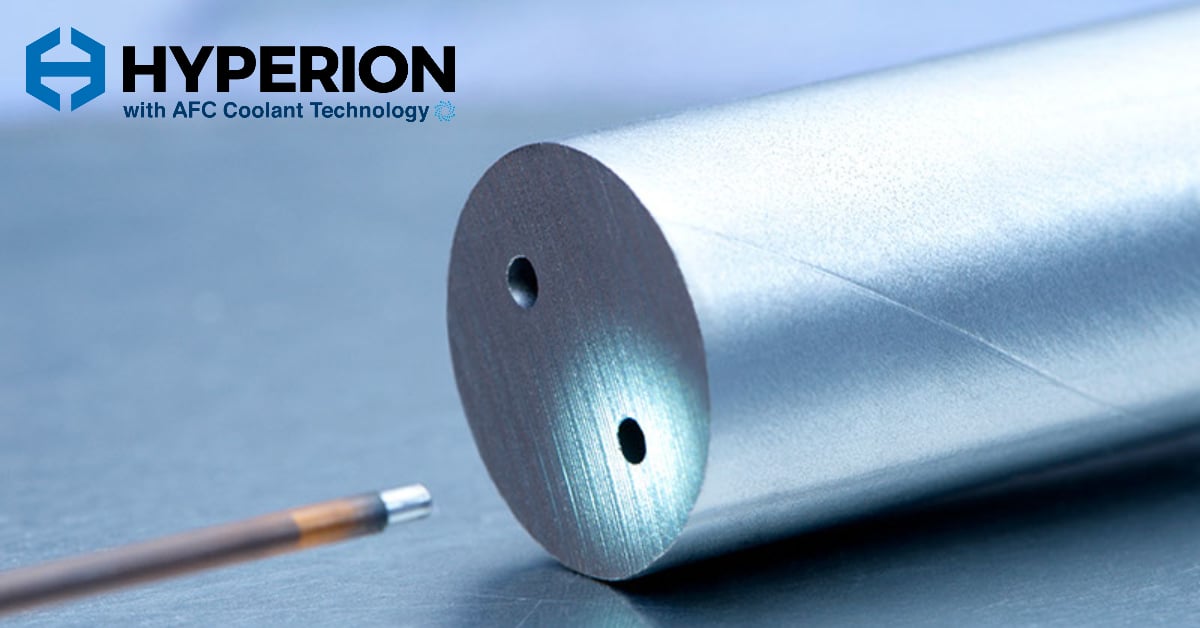
WORTHINGTON, Ohio — Hyperion Materials & Technologies and AFC Hartmetall recently introduced a new product line, Hyperion Grade H10F Carbide Rods with AFC Coolant Technology, that combines the companies’ decades of expertise and innovation to offer toolmakers an optimal solution for drilling and milling applications.
“The development of grade H10F carbide rods with coolant holes is a major step toward our goal of becoming the world’s top independent supplier of cemented carbide rods,” said Ron Voigt, CEO of Hyperion. “When we brought AFC into the Hyperion family at the beginning of the year, we combined our complementary product portfolios and began integrating our businesses to provide our customers with more options than ever with expanded service and support. However, this launch is significant because it is the first product we developed jointly, showcasing how we are stronger together in applying our materials science, engineering and manufacturing expertise to position our customers to win.”
Hyperion, a U.S.-based global leader in engineering and manufacturing advanced materials, has nearly 70 years of experience developing cemented carbide, industrial diamond and cubic boron nitride (CBN) products used in many industries and applications. In January, Hyperion acquired AFC Hartmetall, a Germany-based premium cemented carbide rod manufacturer known for producing tool blanks with innovative coolant holes.
“Hyperion’s grade H10F cemented carbide is widely regarded for its premium quality, unrivaled batch-to-batch consistency, dimensional precision and high performance across a wide variety of applications, including carbide rod blanks for drilling and milling,” said Eduardo Favila, global manager of Hyperion’s Carbide Rods product line. “Our research and development teams did an incredible job learning each other’s processes so they could manufacture Hyperion H10F rods with AFC’s unique coolant hole capabilities. Their accomplishment is even more impressive when you consider the limited opportunities our R&D teams had to collaborate in person because of the global pandemic.”
Favila said toolmakers use carbide rods with coolant holes to manufacture drilling and end milling tools with enhanced performance capabilities. He explained that flowing coolant through the tool itself during the material removal process, in addition to directing coolant onto the tool and workpiece, improves chip removal and heat management at the cutting edge. Combined with the already stellar performance of H10F carbide rods that feature best-in-class geometric and dimensional tolerances, H10F carbide rods with coolant holes enable toolmakers to manufacture tools capable of even greater performance, precision and tool life that also minimize unexpected material failures. These advanced performance capabilities are especially important for those who manufacture products for the aerospace, automotive, medical and electronics industries, he said.
Hyperion and AFC currently offer H10F carbide rods with central (with or without lateral exits), parallel or helical cooling holes in a range of rod diameters, coolant hole diameters, lengths and finishes. Rods also can be customized to meet customers’ needs.
Read more about grade H10F carbide rods with AFC coolant hole technology and use the “PDF Downloads” section at the bottom of that page to access product literature.
Grade H10F carbide rods with AFC coolant hole technology are part of Hyperion’s High Performance Series of carbide rods for toolmakers. The company offers many other carbide rod products for a wide variety of solutions through its Application Specific Series and General Purpose Series.
Learn more by contacting your local Hyperion or AFC representative, and if you do not have one, use the form on our Contact Us page, and we will be in touch.