Hyperion Materials & Technologies modernisiert Produktionsanlage für Hartmetallpulver in Frankreich
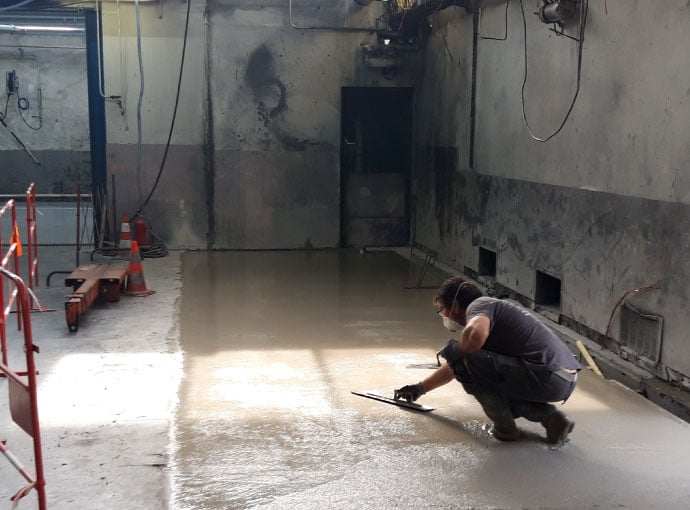
GRENOBLE, Frankreich — Hyperion Materials & Technologies hat kürzlich ein Kapitalverbesserungsprojekt mit einem Umfang von 5 Mio. USD abgeschlossen, das die Kapazität und Leistungsfähigkeit seiner Produktionsanlage für Hartmetallpulver in Grenoble erhöht hat.
Das im April 2018 gestartete Projekt war ein Großprojekt, das die Installation eines zusätzlichen Sprühtrockners und neuer Fräsmaschinen umfasste und die Produktionskapazität des Standorts um rund 40 Prozent erhöhte.
„Diese Upgrades ermöglichen es uns, bei der Versorgung unserer Hartmetall-Produktionsanlagen mit Pressfertige (RTP) Pulver völlig autark zu sein. Sie bieten auch zusätzliche Kapazitäten, um unser RTP-Pulvergeschäft für unsere externen Kunden auszubauen“, sagte John Friederichs, Vice President of Global Operations bei Hyperion. „Dieses Projekt beinhaltete eine umfangreiche Sanierung der Anlage, und wir haben dank der umfangreichen Planung und Koordination zwischen allen Beteiligten ein hohes Maß an Sicherheit und Leistung aufrechterhalten.“
Hyperion kontrolliert viele Variablen während der Pulverproduktion, um seine RTP-Pulver an die Anforderungen spezifischer Anwendungen anzupassen. Hyperion liefert Pulver zu seinen acht Hartmetall-Produktionsstätten auf der ganzen Welt, sowie an andere externe Hersteller.
Das Upgrade-Projekt von Hyperion umfasste mehrere Phasen, einschließlich der Verlagerung vorhandener Fräsmaschinen, um Platz für einen neuen Sprühtrockner zu schaffen, der größer ist als die beiden vorhandenen mittelgroßen Sprühtrockner der Anlage. Das Bauteam baute einen neuen Fräsraum, in dem neue Schleifmaschinen im Attritor-Stil helfen, den Fräsprozess zu beschleunigen. Um den neuen Sprühtrockner zu installieren, musste das Bauteam das Sprühtrocknergehäuse durch eine temporäre Öffnung im Dach auf das Traggerüst heben. Im Rahmen des Projekts installierte, modernisierte und verlagerte das Team auch Versorgungseinrichtungen, installierte einen neuen Laborofen, modernisierte das Brandschutzsystem und die Brandschutztüren und baute einen Waschraum um.
Links: Beginn des Baus eines neuen Raums für Fräsmaschinen. Rechts: nach der Fertigstellung
„Wir haben sowohl externe Auftragnehmer als auch unser internes Wartungsteam eingesetzt, um das Projekt abzuschließen“, sagte Friederichs. „Das Projekt erforderte ein hohes Maß an Know-how, um die gewünschten Ergebnisse termingerecht und sicher zu erzielen. Alle Arbeiten wurden im bestehenden Gebäude koordiniert und abgeschlossen, und die Pulverproduktion wurde nie eingestellt.“
Die Produktionseinheit in Grenoble hat bereits Industrialisierungsversuche mit der neuen Ausrüstung durchgeführt und wird bis Ende des Jahres eine neue Verpackungslinie in Betrieb nehmen.