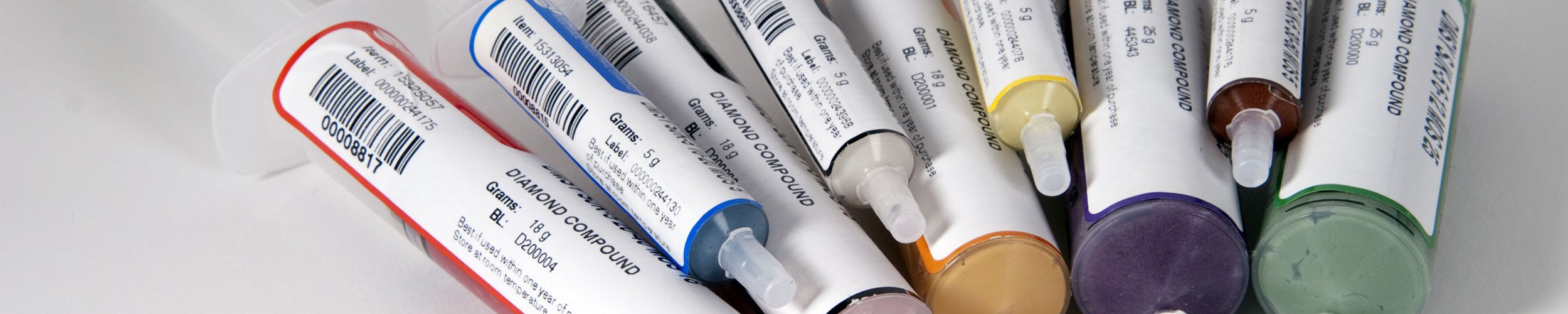
Diamond Compound Paste
Diamond compound paste is comprised of micron-sized synthetic diamonds, natural diamonds, polymicron diamonds, or cBN particles for lapping, polishing, and finishing applications. Diamond paste provides a consistent and high-quality polish, lap, and finish for mold polishing, dies, metallurgical, metalwork, hard disk drives, wire dies, stone & construction, semiconductors, electro-optics, and ceramic applications.
Hyperion offers tailored lapping paste and polishing paste formulations mixed with water-soluble and oil-soluble carriers, providing unique solutions to provide the best performances for each application.
The water-soluble compound paste is best used when exceptional cleaning is required and where petroleum contamination is prohibited. Often it is recommended to use water-soluble products in universities, R&D laboratories, and metallurgical manufacturers where specimen preparation and cross-section analysis are required.
The oil-soluble compound paste is best used for controlled lapping of carbide drawing dies, cold heading dies, and other polishing applications. It is often recommended for use in mold and die polishing.
Hyperion also offers water and oil-based soluble products for achieving more productive lapping results along with facilitation cleaning. Both water and oil-soluble products are necessary for applications where corrosion must be minimized, and oil cannot be tolerated.
Product Groups
Hyperion Code: K700
Application: For use where exceptional cleaning is required
Description: Water soluble compounds available in a variety of synthetic diamonds, natural diamond, and cubic boron nitride (CBN).
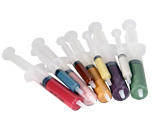
Hyperion Code: K210
Application: For controlled lapping of carbide drawing dies, cold heading dies, and other polishing applications
Description: Oil soluble compounds available in a variety of synthetic diamonds, natural diamond, and cubic boron nitride (CBN).
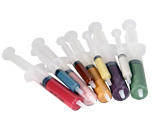
Hyperion Code: G400
Application: Used where corrosion must be minimized but where oil cannot be tolerated
Description: Water/Oil soluble compounds available in a variety of synthetic diamonds, natural diamond, and cubic boron nitride (CBN).
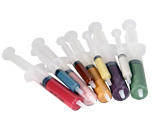
Hyperion Code: K700
Application: For use where exceptional cleaning is required
Description: Water soluble compounds available in a variety of synthetic diamonds, natural diamond, and cubic boron nitride (CBN).
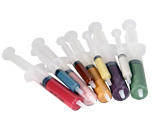
Hyperion Code: K210
Application: For controlled lapping of carbide drawing dies, cold heading dies, and other polishing applications
Description: Oil soluble compounds available in a variety of synthetic diamonds, natural diamond, and cubic boron nitride (CBN).
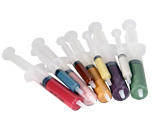
Hyperion Code: G400
Application: Used where corrosion must be minimized but where oil cannot be tolerated
Description: Water/Oil soluble compounds available in a variety of synthetic diamonds, natural diamond, and cubic boron nitride (CBN).
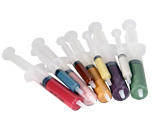
Diamond Paste Applications
Diamond compound paste has unique properties that allow it to be extremely hard, achieving the desired material removal and finishing some of the most challenging workpieces. Diamond paste is a versatile abrasive material that provides a smooth, surface defect-free performance for applications such as cutting tools, dies, wire dies, semiconductors, molding, ceramics, and more.
The concentration of diamond particles in the paste determines its cutting ability and the surface finish it can achieve. Each application involves a degree of concentration to produce the best surface finish.
Light concentration is used for bringing out a finish in finer sizes with its diamond particles, typically 10-20%. Medium concentration is the most popular version. Its diamond particles, typically 30-50%, provide a high surface removal rate, producing a smooth and uniform surface finish. It brings out a finish from coarse to fine. Heavy concentration is used for surface removal or rough surface finishing. Its diamond particles, typically 60-90%, are used for final polishing and achieve a mirror-like surface finish.
Hyperion offers a wide array of compound paste with diamond and cBN sizes ranging from 1/4 to 60 µm, available in syringe and jar packaging options. Each combination is customized based on the compound concentration level to meet consumers' needs.
Hyperion Materials & Technologies also manufactures slurries & suspensions for effective lapping, polishing, and finishing solutions.
FAQs about Diamond Compound Paste
Diamond compound paste is comprised of micron-sized synthetic diamonds, natural diamonds, polymicron diamonds, or cBN particles manufactured for lapping, polishing, and finishing applications of mold polishing, semiconductors, dies, metallurgical, metalwork, hard disk drives, wire dies, stone & construction, electro-optics, and ceramic applications.
Diamond and cBN paste is different from other abrasive materials because its two of the world's hardest materials, and it is best used for lapping, polishing, or finishing super hard abrasive materials. Diamond compound paste offers the best surface finish and reduces downtime when polishing super hard materials, lessening costs.
Diamond compound paste is used for lapping, polishing, and finishing material applications such as mold and die shops, metallurgical, metalwork, hard disk drives, wire dies, stone & construction, semiconductors, electro-optics, and ceramic applications.
The carriers mixed within diamond compound paste are commonly water-based soluble and oil-based soluble. Each provides unique solutions to offer the best performance for each application.
The oil-soluble diamond compound paste is best used for controlled lapping of carbide drawing dies, cold heading dies, and other polishing applications. It is often recommended for use in mold and die polishing.
Water-soluble diamond compound paste is best used when exceptional cleaning is required and where petroleum contamination is prohibited. Often it is recommended to use water-soluble products in universities, R&D laboratories, and metallurgical manufacturers where specimen preparation and cross-section analysis are required.
Diamond compounds offer unique advantages for several different types of applications. Within semiconductor applications, it provides excellent thermal conductivity. Within dies and wire dies, it provides excellent wear resistance. But the application it is most preferred for is mold polishing. It is very hard and abrasive, so it can remove even the smallest scratches and defects from the mold surface. It also allows the mold to have a very smooth surface to produce high-quality parts.