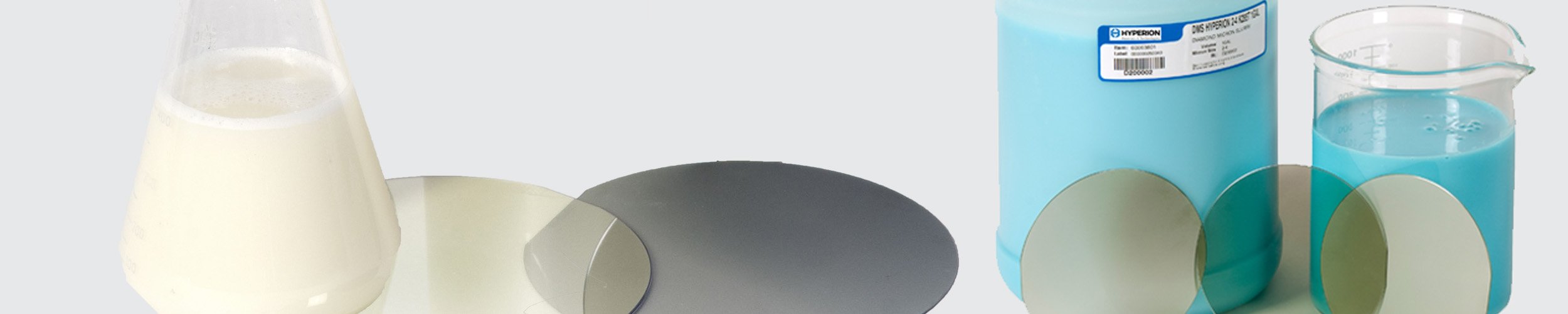
Hyperion Diamond Slurry
Hyperion™ Diamond Slurry is a unique slurry formulation, patented and comprised of synthetic diamond crystals, utilized to improve the lapping and polishing performance of precision applications such as semiconductors, sapphire, metallography, and fine finishing. The diamond used in the slurry is unique, containing multiple fine cutting points for reducing surface roughness when lapping and polishing semiconductor wafers.
Hyperion Diamond slurries achieve greater performance over monocrystalline and polycrystalline micron diamond slurries because they deliver a remarkable material removal rate with the added benefit of an excellent surface finish. Also, with its availability in sub-micron sizes, Hyperion diamond slurries can be tailored to optimize performance at various stages of the silicon carbide (SiC) wafer manufacturing process, improving production and significantly reducing scratching or chipping of the wafer.
Product Groups
Hyperion Code: K285T
Application: Lapping (used where exceptional cleaning is required but where petroleum contamination cannot be tolerated)
Description: Water-based slurries available in a variety of synthetic diamonds, natural diamond, and cubic boron nitride (CBN).
Product Documentation
Hyperion Code: K285T
Application: Lapping (used where exceptional cleaning is required but where petroleum contamination cannot be tolerated)
Description: Water-based slurries available in a variety of synthetic diamonds, natural diamond, and cubic boron nitride (CBN).
Recent studies have shown that using sub-micron Hyperion Diamond slurry helps provide a faster, more efficient, and more productive process for manufacturing epi-ready SiC wafers. Combining the improved material removal rates and enhanced surface finish earlier in the process, the time required for the final chemical mechanical polishing (CMP) stages of the SiC wafer process can be reduced. With this final CMP stage often viewed as the bottleneck in the SiC wafer process, Hyperion Diamond slurry can play a key role in improving throughput and efficiency.
Hyperion Materials & Technologies offers Hyperion Diamond slurry in various sizes, from sub-micron to 100 micron. The formulations are easy to mix or re-suspend, available in water- and oil-based options, can easily rinse clean from substrates, and are available in 500 ml, liter, and 50-gallon container sizes.
Frequently Asked Questions about Hyperion Diamond Slurry
Hyperion Diamond is a unique, patented synthetic diamond crystal containing more surface cutting points than a typical monocrystalline or polycrystalline micron diamond. It is available in powder, slurry, suspension or compound.
Hyperion Diamond offers several benefits to polishing and lapping non-ferrous materials, such as silicon carbide for semiconductors. Its micro-faceted diamond surface contains small cutting points that increase material removal rates while also reducing the surface roughness of the workpiece. Hyperion Diamonds can better retain their size, which helps maintain effectiveness and provide an exceptional surface finish, all while not easily being crushed. The Hyperion Diamond solution can achieve all these benefits with minimal scratching and chipping.
The Hyperion Diamond products are available in micron sizes, now ranging from 0.25 µm to 100 µm. NOTE: Submicron sizes of less than 1 µm are currently available in limited quantities. Inquire about volumes with your Hyperion sales representative.
The Hyperion Diamond products are designed for lapping, grinding, and polishing non-ferrous materials. Common industries and applications that utilize Hyperion Diamond solutions are semiconductor, metallographic, and fine-finishing applications. The Hyperion Diamond products are an excellent solution for machining silicon carbide in the semiconductor industry because of their high material removal rate and surface finish capacities, helping manufacturers quickly produce more epi-ready wafers with an exceptionally smooth surface, free from scratches, pits, or defects that exhibit remarkable durability and longevity.
The Hyperion Diamond is unique compared to monocrystalline or polycrystalline diamonds because of its patented etched surface that contains more cutting points. This allows for faster and more efficient lapping and polishing. Another key feature of the Hyperion Diamond is that they are more durable and can't be easily crushed compared to monocrystalline and polycrystalline diamonds. Crushed diamonds lose their effectiveness quickly, leading to inconsistent and inefficient polishing.
Hyperion Diamond products are available in several forms, including powders, slurries, suspensions, and compounds. In addition to the diamond characteristics, the slurry formulation can be tailored to optimize performance for specific operating conditions and workpieces. Slurries made with Hyperion Diamond powders can achieve higher material removal rates than other monocrystalline or polycrystalline slurries.
Hyperion Diamond products are utilized through many steps of the Silicon Carbide (SiC) manufacturing process. From grinding the SiC ingot and slicing wafers all the way to the final steps leading up to CMP, Hyperion Diamond products have played a key role as manufacturers look to increase efficiencies and throughput. Specially with the Hyperion(r) Diamond, our slurry is used for lapping by some of the largest players in the market while our new submicron Hyperion Diamond slurries are being used for polishing in an effort to reduce the wafer's final chemical mechanical polishing (CMP) stage. A recent study shows this use of submicron Hyperion diamond slurry could reduce the CMP polishing time by up to 50%.