Silicon Carbide Semiconductors – Materials, Challenges and Solutions
Silicon Carbide Semiconductors
Semiconductors are the backbone of electronic devices, offering a perfect balance of control and miniaturization. Produced as the building blocks for the complex electronic functions that power many devices today, semiconductors are typically developed from pure elements like silicon and germanium or compounds like gallium arsenide. The market demand for semiconductors has experienced a shift, challenging manufacturers to utilize innovative materials to improve productivity.
The ever-increasing demand for semiconductors in various sectors, such as consumer electronics, automotive, and artificial intelligence, has strained manufacturing capacity. Semiconductor manufacturers have experienced rapid technological advancements and supply chain disruptions, leading companies to invest in new fabrication plants and challenging them to find new ways to develop semiconductor chips faster and more efficiently.
Silicon carbide (SiC) has garnered significant attention from semiconductor manufacturers, enabling them to overcome efficiency challenges when machining semiconductors. SiC is a wide-bandgap semiconductor material that can operate at higher temperatures and voltages than silicon, making it particularly suitable for high-power and high-temperature applications. Due to its higher thermal conductivity, SiC semiconductors have seen growing adoption in industries such as power electronics, electric vehicles, and renewable energy systems.
Benefits of Silicon Carbide
The silicon carbide device market is projected to reach up to $14 billion by 2030, at an estimated 26% CAGR. Driven primarily by the high projected growth in electric vehicles, solar and wind energy, and smart grid power switching, the demand for silicon carbide is skyrocketing. Although silicon is still predominantly used in the market today, silicon carbide offers several advantages over silicon for semiconductor manufacturers, including:
- Higher Efficiency – Silicon carbide has a wider bandgap compared to silicon allowing it to operate at higher temperatures and voltages, leading to better efficiency rates and lower power losses for manufacturers.
- Higher Power Density – SiC semiconductors handle a higher power density than silicon, maintaining more power in a smaller package.
- Higher Frequency Operation – With a higher thermal conductivity than silicon, silicon carbide can handle extremely high temperatures, making it suitable for high-temperature aerospace and automotive applications.
- Longer Lifespan—Due to their unique properties, such as excellent thermal conductivity, wide bandgap, high electron mobility, and high power density, SiC semiconductors last longer than silicon. By switching to silicon carbide, manufacturers’ products require less maintenance and replacement over time.
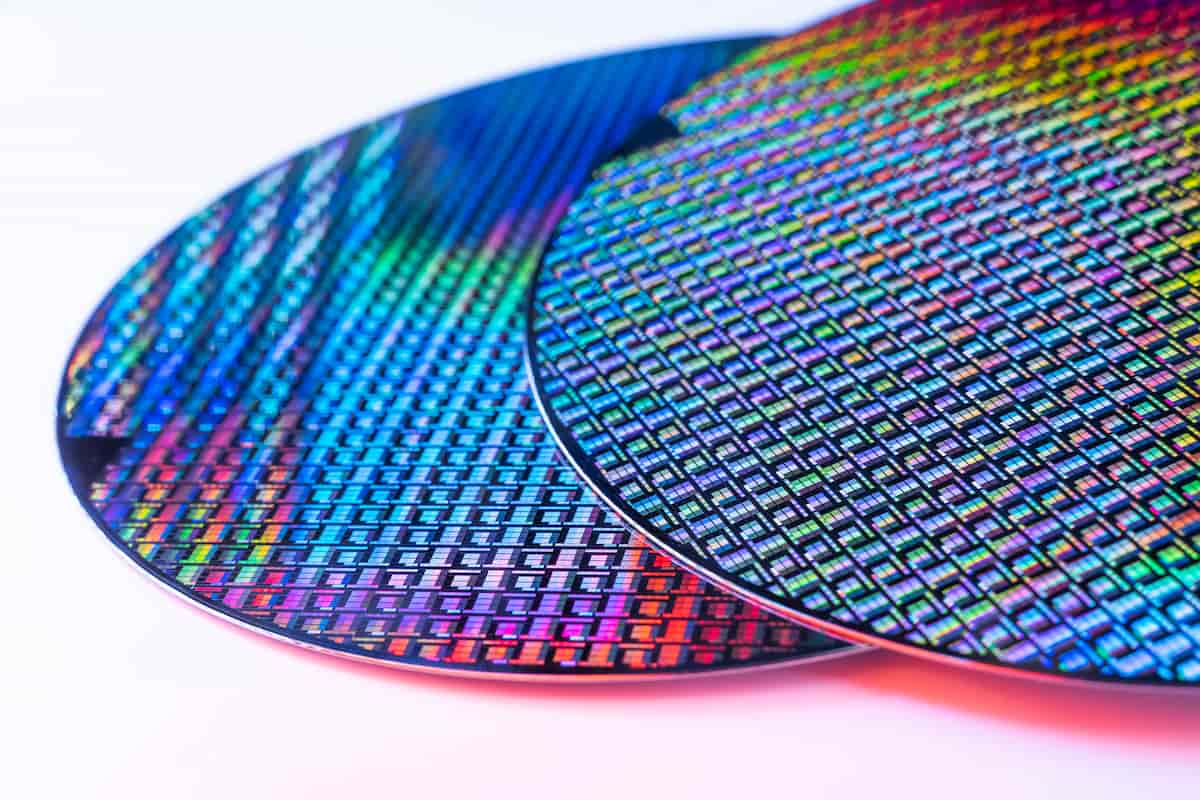
Machining Silicon Carbide
Machining SiC material for semiconductor manufacturers can be challenging due to its unique material properties. Silicon carbide is extremely hard and brittle, perfect for semiconductors, but difficult to machine with many materials. Applying excessive force when machining with improper materials can cause cracks, defects, and chipping of the SiC, rendering it unusable for precise semiconductor components.
SiC wafer manufacturers depend on the best material to maximize their throughput and productivity, which is why synthetic industrial diamonds are ideal for machining silicon carbide.
Diamond, renowned as the hardest material in the market, stands as one of the most effective options for machining SiC. The diamond grit, with proper size, strength and cutting edges, facilitates precise machining on delicate SiC wafers. With reduced brittleness and exceptional thermal conductivity, diamond significantly lowers the risk of inducing cracks or fractures, which is vital in dissipating the heat generated during machining, thereby averting excessive temperatures that could potentially harden the silicon carbide material.
Hyperion Solutions that Serve the Silicon Carbide Semiconductor Industry
Hyperion Materials & Technologies is born out of GE, Diamond Innovations, and Sandvik Hard Materials. Research and development is our foundation, and partnership with our customers to create innovative technologies is the source of our continued growth. With over seven decades of developing hard and super hard materials, Hyperion provides a full range of synthetic industrial diamonds uniquely suited to help machine silicon carbide wafers for the semiconductor industry. Available in sizes from sub-micron, micron, and mesh, Hyperion’s diamond portfolio offers several benefits for precision machining applications, including:
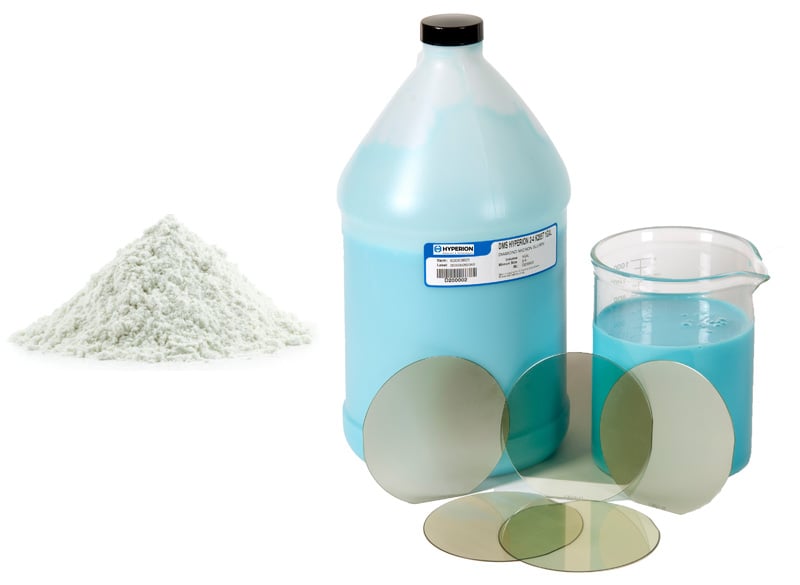
- Enhance SiC Performance and Throughput – Hyperion offers unique submicron and micron diamond options with more fine cutting points than monocrystalline or polycrystalline micron diamonds. With more cutting points, Hyperion's unique diamond solutions help increase the material removal rates while reducing the surface roughness of the silicon carbide wafer.
- Unmatched Durability and Control – Hyperion’s micron diamonds are not easily crushed and maintain their size and effectiveness throughout the SiC machining process, providing exceptionally durable and consistent edges.
- Exceptional Edge Quality – Hyperion's submicron and micron solutions are characterized by their sharp edges, crucial in minimizing tool wear and tear. Exceptional edge quality increases manufacturing flexibility, extended tool life, and enhanced control and precision, making Hyperion's solutions a top choice for lapping and polishing applications.
- Excellent Wafer Surface Quality – Hyperion offers unique micron diamonds that can detect oversized particles. These particles can cause chipping, scratching, and imperfections in the wafer, leading to its total loss.
Products for Silicon Carbide Semiconductors
Hyperion offers several diamond products that serve the semiconductor industry.
Hyperion Diamond Slurry
Hyperion Diamond slurry is a patented, unique micron diamond slurry and suspension designed to enhance the lapping and polishing performance in precision applications such as silicon carbide wafer processing. With the included diamond containing a modified surface of several fine micro-cutting points that drastically reduce a workpiece's surface roughness, Hyperion Diamond slurry helps provide a faster, more efficient, and more productive process for manufacturing epi-ready silicon carbide wafers.
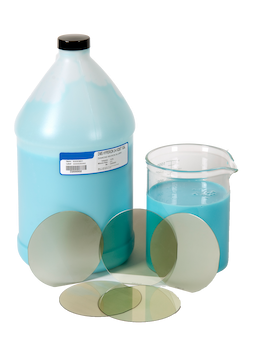
Micron Diamond Powders
Superabrasive diamond powder provides unprecedented material consistency, cutting performance, and surface quality for polishing and lapping wire saw, sapphire, glass, and ceramic applications. Hyperion offers micron diamond powder ranging from submicron to 50 microns, available in metal and resin bond and with a patented etched-diamond surface. Hyperion’s micron diamond powders are used in abrasive tools to produce a finish that is finer and smoother than other abrasive materials, making them ideal for precision grinding wheels and polishing pads.
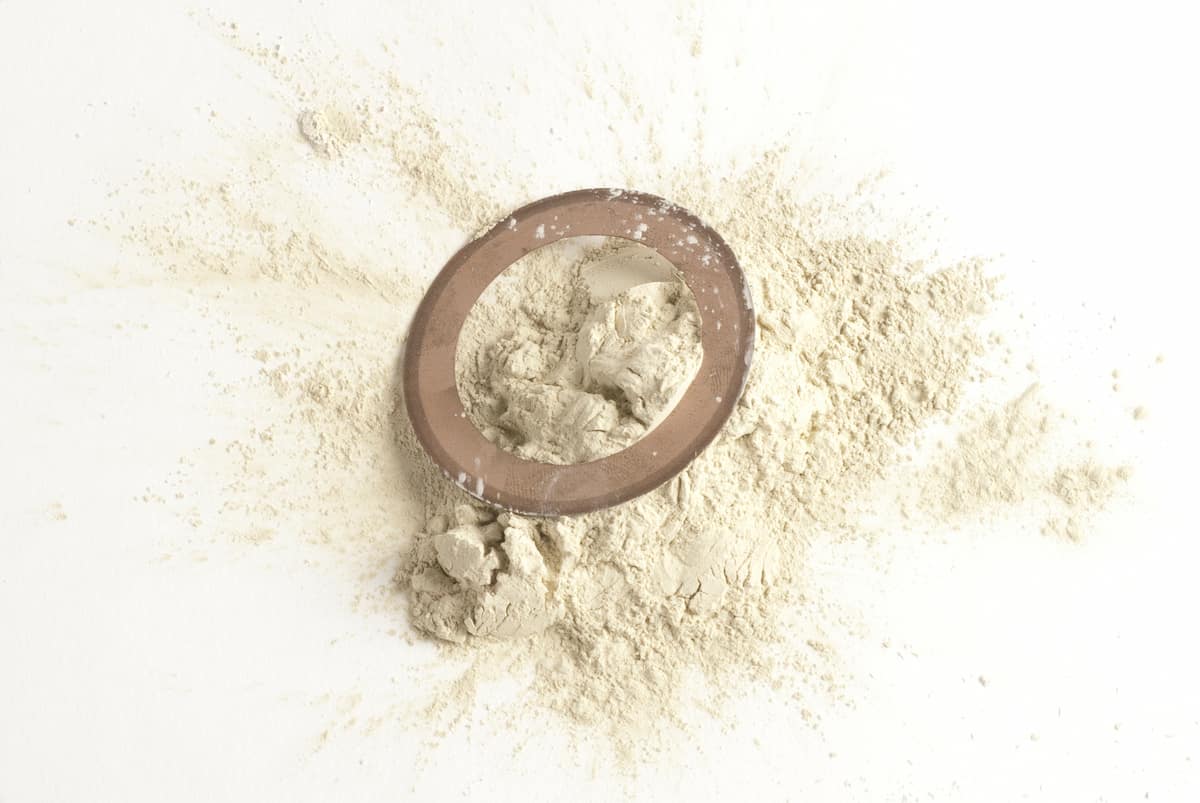
Learn more about Hyperion’s synthetic diamond solutions for machining semiconductors and discover how it can boost SiC wafer production by reducing CMP polishing up to 50%.