RVG™ Diamond Abrasives
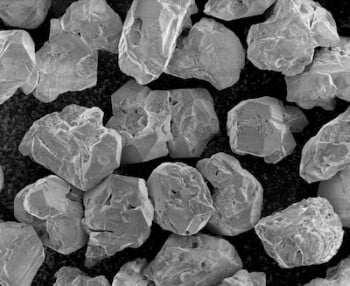
Hyperion Series: RVG
Product Type: Resin and Vitrified Bond Diamonds
Description: Engineered to provide optimum performance in all bond systems, from phenolic resin to high-temperature polyimide resin and vitrified bonds. RVG diamond abrasives grind challenging materials such as tungsten carbides, glass, technical ceramics, and electronic components.
RVG™ diamond abrasives are synthetic diamonds designed to enhance grinding wheels' performance in challenging machining applications. Commonly used for tools that grind tungsten carbide, glass, technical ceramics, reinforced ceramics, and other non-ferrous applications, RVG abrasives achieve considerably higher material removal rates and excellent surface finish in wet or dry grinding modes compared to other resin and vitrified bond solutions.
Resin and Vitrified Bond Diamond Advantages
Resin Bond Diamonds are highly cost-effective abrasives that significantly increase the grinding wheel’s productivity and workpiece quality, enabling toolmakers to develop consistent high-performance tools that provide exceptional workpiece dimensional accuracy and surface integrity while minimizing total cost per part.
Longer-Lasting Grinding Wheels
One of the most significant cost factors in a grinding operation is the relationship between wheel performance and the costs incurred to attain optimal performance capabilities. RVG diamonds help enhance the material removal rate while decreasing the abrasive concentration on the "cutting zone," leading to slower grinding rates and longer cycles when grinding challenging materials. Wheel manufacturers can count on their wheels, offering tool users a predictable grinding output, leading to faster turnaround times and higher productivity.
Deliver Superior Surface Integrity
With proprietary processes for producing each RVG abrasive grade, toolmakers achieve a more robust edge finish for their workpieces. Tool users can count on utilizing the resin and vitrified grinding wheels to produce cleaner and faster cuts while minimizing scrap waste.
Resin and Vitrified Bond Diamond Abrasive Solutions

RVG High Diamond Toughness Abrasives
Diamond grades that are designed for grinding wheel applications.
Hyperion offers several different resin and vitrified bond grinding diamond abrasives, from highly friable to extremely tough diamonds. Each product specifically focuses on providing exceptional bond grinding performance for non-ferrous material tools.
RVG High Friability Diamond Abrasives
Designed for carbide, PCD, ceramic, and cermet grinding, Hyperion produces highly friable resin and vitrified bond abrasives for exceptional bond retention and surface roughness.
RVG® 800 Diamond
Hyperion’s RVG 800 diamond offers superior free-cutting capabilities due to the controlled micro-fracturing of the crystals. Available uncoated or coated, RVG 800 is suitable for applications with demanding tolerance requirements. It achieves consistent surface finishes and accurate geometries in grinding tungsten carbides, Cermets, and technical ceramics.
RVG® 810 Diamond
RVG 810 is an uncoated diamond ideally suited for high-precision grinding in demanding materials with stringent quality requirements. RVG 810 is extremely effective where wheel life and form retention are critical.
RVG® 810D Diamond
Hyperion offers a coated version of RVG 810 called RVG 810D. Consisting of a 50% copper-based alloy coating, RVG 810D is a highly friable crystal ideal for grinding dry phenolic or wet polyimide carbides and polycrystalline diamond (PCD) materials.
RVG® 880 Diamond
Coated in a 56% spike nickel-based solution, the RVG 880 crystal offers even more improved free cutting and fracture characteristics, requiring lower grinding ratios and providing wheel manufacturers with extended wheel life. The spike nickel diamond's textured coating enhances crystal retention while extracting heat from the grinding interface. RVG 880 is highly suitable for wet grinding cemented carbide and reinforced ceramic workpieces.
RVG® 890 Diamond
Hyperion offers a nickel-based coating option of the RVG 810 called RVG 890. Coated in a 56% spike nickel-based solution, the RVG 890 crystal is the most productive in the RVG diamond family. Boasting excellent free-cutting characteristics, RVG 890 offers a controlled microfracturing mode while providing superior surface finishes. RVG 890 diamond is unparalleled in part-to-part consistency regarding technical ceramics, Cermets, and new challenging to grind materials.
RVG Medium Toughness and Friability Abrasives
Developed with a nice balance of toughness and friability, Hyperion offers RVG, RVG 2 and SPR series diamond abrasives for workpieces in wet grinding, carbide and ceramics.
RVG® W Diamond
RVG W diamond is designed for and highly successful in wet grinding applications. Containing a 56% nickel-based alloy coating, RVG W is universally applicable and the most widely used diamond phenolic bond on the market today. With enhanced bond retention and heat dissipation, RVG W diamond enables a prolonged tool life for grinding wheels.
RVG® W30 Diamond
RVG W30 diamond, a 30% nickel-based alloy coating, offers wheel manufacturers a choice that blends free-cut only RVG diamonds and longer wheel-life RVG W diamonds. RVG W30 achieves a perfect balance between long wheel life and low power consumption and is often used in tungsten carbide tool grinding.
RVG® D Diamond
A copper-based alloy coating with a 50% copper coating, the RVG D Diamond is best used in grinding applications where temperature control is necessary. Due to its excellent thermal conductivity, it is widely used in demanding wet and dry tool room applications.
RVG® WS60 Diamond
RVG WS60, spike nickel-based diamond coated up to 60%, is specially designed for improved bond retention in wet grinding applications, specifically water-based coolants. Due to its highly thermal-resistant metallic spikes, RVG WS60 contains excellent thermal stability, making it ideal for applications with long contact lengths, such as flute grinding of tungsten carbide drills and face grinding of technical ceramics. RVG WS60 offers wheel manufacturers a significantly longer lifespan than other nickel-based solutions. Explore more by reading "How Spike Nickel Diamond Coatings Enhance Ceramic Grinding."
RVG® NS56 Diamond
Developed for general-purpose applications, Hyperion's RVG NS56 diamond contains a 56% spike-nickel based coating engineered to expand bond retention in a workpiece. Universally applicable in all wet grinding applications, RVG NS56 offers exceptional grinding performance in both phenolic and polyamide bond systems.
RVG® AG50 Diamond
RVG AG50, a friable diamond with irregular shapes and a spike silver coating, is specially developed with a 50% silver coating for tungsten carbide flute grinding with straight oil coolant. Its unique design enhances bond retention, adds lubricity, and quickly dissipates heat from the cutting zone. Using straight oil as a coolant, RVG AG50 can eliminate carbide cracking, smoke generation, and a short wheel life. Additional benefits of RVG AG50 are its ability to perform effectively at low wheel speeds and decreased power requirements, prolonging tool life.
RVG® 2 Diamond
RVG 2 diamond is an uncoated, medium-grade resin bond diamond that offers wheel manufacturers a product with controlled fracturing and self-sharpening properties that lead to excellent free cutting. RVG 2 is designed for grinding wheel applications that require better performance than that of an economy-grade resin bond diamond.
RVG® 2-W Diamond
The RVG 2-W is the coated version of Hyperion's RVG 2 resin bond diamond, containing a 56% nickel-based alloy coating. With an enhanced nickel coating that improves bond retention, RVG 2-W is ideal for wet grinding of ceramics and tungsten carbides, enabling wheel manufacturers to achieve longer tool life and consistent performance.
SPR® Diamond
The SPR diamond is an economy-grade grinding diamond used for less demanding applications where abrasive cost is the primary consideration. Its friability enables controlled diamond fracturing, wheel self-sharpening, and free-cutting action.
SPR® N Diamond
Designed with a 56% nickel-based alloy coating, the SPR N diamond is a standard nickel coating that improves retention and heat dissipation in the bond, ultimately resulting in longer wheel life.
SPR® N30 Diamond
Similar to Hyperion's SPR N diamond, SPR N30 is a nickel-based alloy with a 30% coating level. It reduces the grinding wheel's energy and heat generation while maintaining a minimal reduction in wheel life.
SPR® CU50 Diamond
SPR CU50 is a copper-coated alloy diamond with a 50% coating level. The copper coating increases the thermal conductivity of the wheel rim while improving heat dissipation. SPR CU50 diamond prevents thermal workpiece damage in dry grinding applications.
SPR® NS56 Diamond
SPR NS56 is a spike nickel-based coating with a 56% coating level. With a unique micro spike structure, the nickel-based coating is designed to increase crystal retention in the bond system and can reduce crystal concentration compared to standard coatings, providing additional value.
RVG High Diamond Toughness Abrasives
Highly tough resin and vitrified bond diamond grades that are designed for grinding wheel applications used within carbide, PCD, and heavy-duty grinding.
RVG® CSG-II Daimond
A very tough diamond, the RVG CSG-II is a nickel-based alloy with a 55% coating level that reduces wheel loading and minimizes workpiece burning when grinding tungsten carbide and steel combinations. Due to its toughness and impact resistance, RVG CSG-II diamond is highly recommended for heavy-duty grinding and applications with interrupted cutting.
RVG® RB-I Diamond
RVG RB-1 diamond is an uncoated diamond best suited for applications requiring free-cutting capabilities, low-cutting forces, and thermal stability are required. Common applications that utilize RVG RB-1 diamonds are tungsten carbide and PCD grinding.
RVG® RB-II Diamond
RVG RB-II Diamond is a nickel-based alloy with a 56% coating that generates excellent grinding results in applications that sustain interrupted cuts. The blocky crystal form provides extended tool life to grinding wheels in applications where high material removal rates are necessary to grind challenging materials. RVG RB-II diamond is recommended for tungsten carbide and PCD grinding.
RVG® RB-II 30 Diamond
RVG RB-II 30 is also a nickel-based alloy coating, similar to RB-II diamond; however, it has a lower coating level of 30%. RVG RB-II 30 diamond abrasives provide lower grinding energy and heat dissipation, ideally suited for applications that balance wheel life and grinding energy.
RVG® RB-D Diamond
RVG RB-D diamond, a blocky crystal with a 50% copper coating applied, provides excellent performance in dry grinding or wet polyimide, tungsten carbide, and PCD grinding.
Resin Bond Diamond Abrasives MESH/FEPA Properties
Mesh Size
(FEPA Size)
|
60/80 (D252) | 80/100 (D181) | 100/120 (D151) | 120/140 (D126) | 140/170 (D107) | 170/200 (D91) | 200/230 (D76) | 230/270 (D64) | 270/325 (D54) | 325/400 (D46) | 400/500 |
---|---|---|---|---|---|---|---|---|---|---|---|
CSG-II | ✔ | ✔ | ✔ | ✔ | ✔ | ✔ | ✔ | ✔ | ✔ | ✔ | N/A |
RB-I | ✔ | ✔ | ✔ | ✔ | ✔ | ✔ | ✔ | ✔ | ✔ | ✔ | ✔ |
RB-II | ✔ | ✔ | ✔ | ✔ | ✔ | ✔ | ✔ | ✔ | ✔ | ✔ | ✔ |
RB-II 30 | ✔ | ✔ | ✔ | ✔ | ✔ | ✔ | ✔ | ✔ | ✔ | ✔ | N/A |
RB-D | ✔ | ✔ | ✔ | ✔ | ✔ | ✔ | ✔ | ✔ | ✔ | ✔ | N/A |
RVG | ✔ | ✔ | ✔ | ✔ | ✔ | ✔ | ✔ | ✔ | ✔ | ✔ | ✔ |
RVG NS56 | ✔ | ✔ | ✔ | ✔ | ✔ | ✔ | ✔ | ✔ | ✔ | ✔ | ✔ |
RVG W | ✔ | ✔ | ✔ | ✔ | ✔ | ✔ | ✔ | ✔ | ✔ | ✔ | ✔ |
RVG W30 | ✔ | ✔ | ✔ | ✔ | ✔ | ✔ | ✔ | ✔ | ✔ | ✔ | · |
RVG D | ✔ | ✔ | ✔ | ✔ | ✔ | ✔ | ✔ | ✔ | ✔ | ✔ | N/A |
RVG WS60 | ✔ | ✔ | ✔ | ✔ | ✔ | ✔ | ✔ | ✔ | ✔ | ✔ | ✔ |
RVG 800 | ✔ | ✔ | ✔ | ✔ | ✔ | ✔ | ✔ | ✔ | ✔ | ✔ | N/A |
RVG 810 | ✔ | ✔ | ✔ | ✔ | ✔ | ✔ | ✔ | ✔ | ✔ | ✔ | N/A |
RVG 810D | ✔ | ✔ | ✔ | ✔ | ✔ | ✔ | ✔ | ✔ | ✔ | ✔ | N/A |
RVG 880 | ✔ | ✔ | ✔ | ✔ | ✔ | ✔ | ✔ | ✔ | ✔ | ✔ | N/A |
RVG 890 | ✔ | ✔ | ✔ | ✔ | ✔ | ✔ | ✔ | ✔ | ✔ | ✔ | N/A |
RVG 2 | ✔ | ✔ | ✔ | ✔ | ✔ | ✔ | ✔ | ✔ | ✔ | ✔ | ✔ |
RVG 2-W | ✔ | ✔ | ✔ | ✔ | ✔ | ✔ | ✔ | ✔ | ✔ | ✔ | ✔ |
RVG AG50 | N/A | ✔ | ✔ | ✔ | ✔ | ✔ | ✔ | ✔ | ✔ | ✔ | N/A |
SPR | ✔ | ✔ | ✔ | ✔ | ✔ | ✔ | ✔ | ✔ | ✔ | ✔ | ✔ |
SPR N | ✔ | ✔ | ✔ | ✔ | ✔ | ✔ | ✔ | ✔ | ✔ | ✔ | ✔ |
SPR N30 | ✔ | ✔ | ✔ | ✔ | ✔ | ✔ | ✔ | ✔ | ✔ | ✔ | ✔ |
SPR CU50 | ✔ | ✔ | ✔ | ✔ | ✔ | ✔ | ✔ | ✔ | ✔ | ✔ | N/A |
SPR NS56 | ✔ | ✔ | ✔ | ✔ | ✔ | ✔ | ✔ | ✔ | ✔ | ✔ | ✔ |
For additional convenience, Hyperion also offers a global network of sales, customer service, and technical support experts to help guide customers throughout the entire process. Within customer support, Hyperion provides testing, fabrication, and application development support through its R&D center in Worthington, Ohio.
Hyperion also offers PDS Diamonds for mass tooling solutions, MBS Diamonds for highly specialized tooling solutions, MBH diamonds for metalworking applications, and MBG diamonds for grinding non-ferrous materials. Discover the diamond abrasive materials that best suit your machining needs.